Injection Mold Design
Guidelines
Maximizing Performance Using Copper Alloys
By Dr. Paul Engelmann and Bob Dealey
for the Mold Marketing Task Group of the Copper Development Association |
Copper Alloys for Conveying Plastic
In Injection Molds
The high thermal conductivity of copper alloys makes them ideal materials for the
injection mold sprue bushing and runner bars. Three alloys typically are utilized for the
mold components, which will have contact with plastic. The copper alloys are:
- C17200, high hardness beryllium-copper alloy
- C17510, high conduct beryllium-copper alloy
- C18000, NiSiCr hardened high conductivity copper alloy
These Copper alloys have six to nine times greater heat transfer rates
than conventional mold steels as indicated by the thermal conductivity. |
The sprue or runner system must never control the cooling phase and/or
overall molding cycle. Plastic in contact with copper alloys will set the sprue and runner
faster, allowing more efficient ejection or removal by sprue pickers or robots. |
Mold
Material |
Thermal
Conductivity
(Btu/Hr/Ft2/0F) |
C-17200
C-17510
C-18000
H-13
P-20
420 SS |
60
135
125
17
20
14 |
|
|
Sprue Bushing Radius
In North America two injection mold nozzle and sprue bushing radii are used, 1/2 and 3/4
inch. To insure proper fit up, the nozzle radius is nominal -.015 Inch, while the
sprue radius is nominal +. 015 inch, required tolerances to use.
The sprue or runner system must never control the cooling phase and/or overall molding
cycle. Plastic in contact with copper alloys will set the sprue and runner faster,
allowing more efficient ejection or removal by sprue pickers or robots. |
Nozzle "0" |
Sprue
"0" |
1/16"
1/8"
3/16"
3/8"
5/16"
Nominal |
3/32"
5/32"
7/32"
9/32"
11/32"
+1/32" |
|
Sprue Bushing Orifice Machine nozzle orifices come in nominal 1/16"
fractional inch sizes. To insure that the slug in the nozzle will pull through the sprue,
the orifice must be .031 (1/32 inch) larger in diameter. This dimension is referred to as
the "0" dimension. The relationship is shown in this chart. |
|
Sprue Bushing Taper
To aid in the removal of the sprue from the bushing, a taper of one-half inch per foot is
normally used in injection molding. Calculate the sprue orifice at the parting line face,
multiply the tangent of the taper angle times the length, plus the "02".
Knowing this dimension, informed decisions can be made on primary runner sizing.
The sprue frequently controls the molding cycle when larger orifice conventional steel
sprue bushings are used. The application of a copper alloy sprue bushing cools the sprue
more quickly and efficiently, allowing the molding cycle to be controlled by the piece
part.
Pressure loss is high in the sprue. This is the only place in the feed system where tile
channel progresses from a smaller area to larger. Frequently, smaller orifices are used on
long sprue bushings in an effort to reduce the mass. This results in extremely high
injection pressure losses, making the part hard to fill.
Using a copper alloy sprue bushing allows for an increased size orifice, thus reducing
pressure loss while maintaining reasonable cooling times. |
Sprue Retention and Anti-Rotation
Pressure acting on the parting line face of the sprue, due to projected area of the runner
system or part detail, exerts pressure on the sprue bushing.
Also, a sprue bushing that is not keyed will rotate creating misalignment with the runner
machined into the face of the sprue bushing and the runner system. To prevent these
problems, retain and key the sprue into position with the use of a cap screw.
Sprue Fit Heat must be transferred from the sprue through the copper alloy sprue bushing
to the mold plates. Interference fit is recommended for optimum cooling. The bore through
the "A" plate should be nominal size to plus .0005 inches with a surface finish
of at least 16 RMS. The shank of the sprue bushing should be the nominal size, plus .0005
to plus .001 inches. |
Standard Sprue Bushing Availability
Copper alloy sprue bushings with patented stainless steel nozzle seats are commercially
available. An insulator between the nozzle and sprue is beneficial in controlling
the flow of heat from the nozzle to the sprue. Special sprue bushings may be constructed
to suit using standard 1/2 inch per foot sprue bushing tapered drills and reams. Sprue
bushings with tapers of up to 3/4 inch per foot have been used for difficult to remove
plastics. Care must be taken to insure that the taper is draw polished and free from
undercuts or rough surfaces that could hinder sprue removal. |
Conventional Injection
Mold Runner Systems
The shape of the runner, full round or trapezoidal, or other configuration, is dictated by
mold design. The most efficient runner cross section is full round. The efficiency of the
runner cross section can be calculated with a formula, the larger the ratio the better. |
ER
= A/P |
ER =
Efficiency Ratio
A = Area of runner cross section
P= Periphery of runner cross section |
|
|
Injection Mold Runner Bars
Runner systems for high cavitation molds normally have larger diameters due to runner
balancing. The runner system extends the molding cycles as heat is slowly transferred from
the thick plastic to steel mold plates. Inserting copper alloy runner bars in the mold
"A" and "B" plates, cooling the runner faster, is beneficial, in
reducing the overall molding cycle. |
Runner Sizing
Runner sizing is dependent on many things, including: plastic material: part size, weight
and wall thickness; molding machine capabilities and processing parameters and, the number
and placement of the cavities.
Each mold is unique and the designer must consider all parameters and options available on
an individual case by case basis. Several mold design software packages are available,
including Mold Flow and C-Mold, which address
sizing of the runner system.
One method of runner sizing and balancing used by mold designers starts at the sprue and
then works toward the gate. Other designers start with the part wall thickness and work
back to the sprue outlet orifice. The normally recommended procedure is that, in the
direction of plastic flow, the runner area always goes from larger to smaller. Never from
a smaller area to a larger area. |
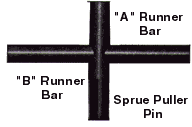 |
When the primary runner diameter is known, the sum of the areas of the multiple
connecting runners must be equal or smaller in area than the preceding runner. When
working back from the part, some designers size the final runner channel size (that runner
which feeds the gate) to equal the thickest wall section in the part. Each runner
intersection then is a function of the area of that runner times the number of connectIng
runners, usually two. Therefore, the area of the upstream runner is always at least equal
to or larger in area than the With the increased cooling rate of sum of the
branches. |
|
Note that a the copper alloys and proper runner with one-half the area is not the
same as a runner of one-half the diameter.
|
Formulas for calculating the area of the runner:
Full Round Runner A = 0.7854
d2
Trapezoidal Runner A=(w1+w2) h/2 |
A=area, d=diameter, l=length, w=width, h=height |
|
|
Runner Bar Mating
Best results are obtained by designing and building the runner bars to have zero to
negative contact with each other when the mold is closed. This will prevent any
deformation on the parting line surfaces that could result from high clamping pressures
exceeding the compressive strength of the alloy. To accomplish this, the "A" and
"B" runner bars should be flush to minus .001 inch on each side of the mold.
This allows the mold base and/ or cavity and core inserts to receive machine clamp force,
not the runner bars.
Care must be taken to understand the characteristics of the plastic being molded and
clearance should be short of allowing the runner system to flash. Additionally, it is
important to insure that the mating halves of the runner system are in perfect alignment,
with no mismatch at the parting line, to maximize plastic flow efficiency |
Runner Bar Cooling
The runner system must never control the molding cycle. To insure proper temperature
control of the runner bars, cooling channels should be placed directly into the both the
"A" and "B" side inserts. The cross-drilled holes should be blocked
with a plug containing an "0" ring and a straight thread plug. Due to the high
thermal conductivity of the copper alloys and the tendency to thermal cycle rapidly,
tapered thread systems must be avoided in the copper alloys to prevent cracking.
With the increased cooling rate of the copper alloys and proper cooling arrangements,
larger diameter runners can be used in a mold equipped with copper alloy runner bars.
Almost without exception, runner diameters one or two sizes larger can be set up quicker
with the copper alloys, over traditional mold steels. |
Sprue Puller
A reverse taper sprue puller, 30 for stiffer materials
and 50 for flexible materials, is recommended to insure
sprue removal. To rapidly cool the undercut machine, the puller directly into the runner
bars or a copper alloy insert. |
|
Acknowledgments
The injection mold design guidelines were written by Dr. Paul Engelmann, Associate
Professor Western Michigan University and Bob Dealey, Dealey's Mold Engineering, with the
support of Dr. Dale Peters, for the Mold Marketing Task Group of
the Copper Development Association. Kurt Hayden, graduate research assistant. WMU
generated the illustrations. Research conducted by WMU students in the
plastics program. |
|
Disclaimer
These guidelines are a result or research at WMU and industry experience gained with the
use of copper alloys in injection molding. While the information contained is deemed
reliable, due to the wide variety of plastics materials, mold designs and possible molding
applications available, no warranties are expressed or implied in the application or these
guidelines. |
|
SITE INDEX
|
Disclaimer
While the information contained is deemed reliable, no warranties are expressed or
implied. For specific information regarding an application please call 1-800-272-3031 or
e-mail us at sales@moldstar.com
|
|
Copyright © 2024 by Performance Alloys &
Services, Inc
Web site hosted by Network Solutions
All Rights Reserved.
|